Preventing Catastrophe: Understanding Steam Explosions in Molten Material Environments
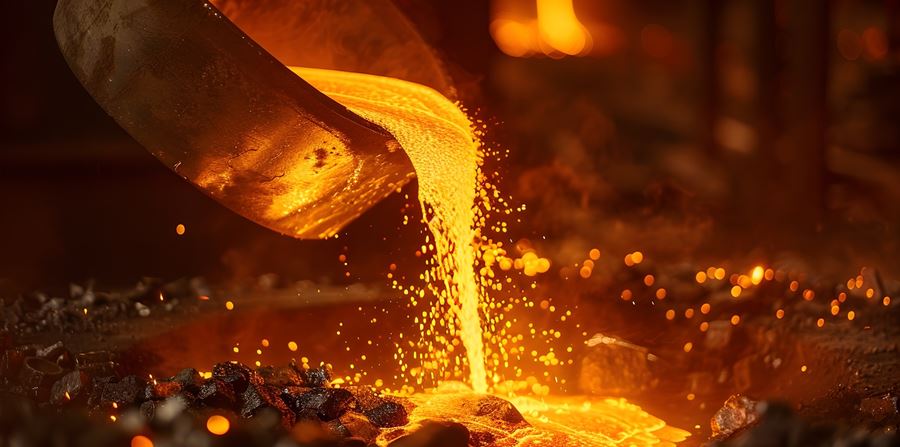
Handling molten materials is a critical part of production processes in various industries, whether in metal refining, glass production, or other high-temperature operations. Water is commonly used for cooling in these environments due to its excellent thermal properties. However, this practice comes with significant risks. Leaks in cooling systems can lead to dangerous steam explosions, causing severe damage to equipment and facilities and potentially resulting in fatalities.
Although catastrophic incidents are relatively infrequent, the potential for severe consequences necessitates a thorough understanding of these risks. This article delves into the science behind steam explosions and industry best practices for design and monitoring, and provides real-world case studies to underscore the importance of proper engineering and preventive measures.
Uses of Water in Molten Material Environments
Water is a common process material used in many molten materials or pyrometallurgical environments. It is readily abundant, highly thermally conductive, and has a very high heat capacity. As such, it is a common cooling medium used in molten material processing equipment.
Molten material handling equipment can often experience temperatures over 2000°C. Even the most robust refractory materials can quickly degrade at these temperatures, especially if they are subject to additional forms of wear (abrasion, chemical, etc.). Given this very aggressive environment within molten material equipment, design engineers will often design external cooling systems in the vessel lining to try to freeze some of the internal process material onto the hot face of the equipment lining. Once frozen, this material acts as a primary line of defense against the wear of the vessel’s lining.
However, due to several variables, this lining can still degrade, and in some instances, far enough that water begins to leak directly into the vessel. These leaks are hazardous and can quickly cause steam explosions, leading to significant damage to the equipment and the surrounding building and, in some instances, fatalities.
The risk of steam explosions due to leaks is always present at the onset of the leak. The magnitude and probability of an explosion can vary based on where the leak is occurring and its size; however, the risk of a serious explosion is always present when there is a leak.
The Science Behind Steam Explosions
A steam explosion is caused by a sudden vaporization of water into water vapour (steam) without providing a path for the water vapour to escape or depressurize. When water undergoes a phase change from liquid to gas, it experiences a change in total volume. In an unconstrained setting (i.e., where the water or steam is not forced to occupy a specific volume), 1g of water, equivalent to 1mL in volume, is converted to 1g of steam. That steam would have a theoretical approximate volume of 1671mL, representing a volumetric change of a factor of 1671.
If the steam is constrained, the resulting pressure can cause the vessel or container to explode violently if it cannot withstand this sudden change in pressure.
Global Statistics and Industry Standards
No currently available global data details the total number of steam explosions and their severity. This is not unusual, as steam explosions can and have happened across various industries that all use this cooling method. Iron and steel making, ferrous metals, copper, aluminum, and nickel, among other industries, all use different forms of molten material reactors to process and refine, many of which are cooled using water.
However, several industry best practices for designing and operating water-cooled systems help reduce and mitigate risk from steam explosions.
Proper Design
Proper design of water-cooled elements and water-cooling systems is the first line of defense in mitigating the risk of steam explosions. Properly designing these systems involves developing finite element models subjected to several different thermal loading conditions to determine the “freeze line,” even in worst-case scenarios. This design method is crucial to ensure the system is adequately designed and provides a basis for temperature alarms, making the system predictive before a leak occurs. This works by establishing a temperature point based on the position of the temperature sensors (thermocouple), which, if exceeded, would indicate that the cooling system has experienced wear beyond its design and is at risk of developing a water leak.
Proper Monitoring Controls
Typical best practices for monitoring water leaks can be followed before and after a leak begins. Before the leak, temperature sensors can be used to monitor the condition of the cooling system continuously. After a leak has occurred, plant operators have several options for safely determining if a leak is present.
Option 1: Flow Monitoring
Flow monitoring is the most common option for leak detection, using a flowmeter on supply and return lines for the cooling system. If the flowmeter readings remain steady and match each other, no leak is present. If the return line flowmeter reads less than the supply line, a leak is in the system.
Option 2: CCTV
Closed-circuit television systems (CCTV) are common but not as reliable as flow monitoring. CCTV provides operators with visual feedback on the vessel, and potential leaks can be seen on the screen. The drawback of CCTV is that it is difficult to use reliably within the molten material vessel, even with high-temperature-resistant cameras, as dust and material can quickly accumulate on the camera's screen.
Alternative Cooling Systems
The final solution to mitigating the risk of steam explosions in molten material reactors would be eliminating water altogether. Alternatives include air cooling systems, although some new novel cooling systems use molten salt as an alternative. Both cooling mediums completely eliminate the risk of steam explosions; however, each has drawbacks. In the case of air-cooling systems, the effectiveness of the cooling system is greatly reduced (often to the degree that it is not a viable cooling system). Whereas a molten salt system is much more expensive than a water-cooled system.
Normalization of Leaks in the Industry
As experts in this field, we have experience working with operators from small-scale refineries to major billion-dollar refineries worldwide. This experience reveals a tendency to normalize the risk of steam explosions in the industry. Due to the essentiality of cooling water systems and the aggressiveness of the equipment, leaks can often occur. Most leaks never cause a steam explosion and the ones that do often cause minor explosions or pops, with little to no consequences beyond minor damage to the equipment. Over time, this causes plant operators and owners to normalize and accept water leaks in their operations as they have, in some cases, decades of operating with leaks with no issue. This is not prudent engineering practice, if one evaluates this risk on a typical quantitative risk analysis matrix (Figure 1), the consequence will always be considered (5: Catastrophic), as an incident can cause complete destruction of a plant and fatalities. As such, no matter the probability or likelihood of the event, the risk must always be considered moderate or even high (depending on a plant’s individual risk profile) and, must always be planned for.
Figure 1: Typical Risk Evaluation Matrix
Case Study: Carbide Industries, Louisville, KY, USA
In March 2011, a steam explosion in the electric arc furnace killed two employees of Carbide Industries. The explosion ejected solid and powdered debris, flammable gases and molten calcium carbide at temperatures over 2100°C. The hot gas and debris broke through the double-pane reinforced glass window of the plant control room, severely burning the two workers inside. These workers succumbed to their injuries within 24 hours of the incident.
The U.S. Chemical Safety and Hazard Investigation Board (CSB) investigated the event. Although they could not determine the exact cause of the incident, they proposed several plausible scenarios based on interviews, plant records, and knowledge of the carbide process.
Examinations of the furnace roof revealed that a significant portion had been experiencing water leaks. These types of leaks in furnace roofs are not uncommon, as this furnace region experiences a high heat load and abrasion from gas flow in the area. Additionally, many furnace roofs (including the EAF at Carbide Industries) are made as built-up steel channels where water is pumped through these built-up channels. This can often cause “dead zones” where cooling is drastically diminished.
CSB noted that Carbide Industries had executed 26 leak repairs four months before the March incident. CSB also noted a normalization of leaks and minor explosions in the plant in the 20 years before the incident, including in 1991, when an explosion blew the window out of the plant control room, and in 2004 when another explosion damaged the same window.
Due to this normalization, CSB noted that Carbide Industries did not adequately perform root cause evaluations of previous explosions. These evaluations could have identified the need to relocate the furnace control room so that it was not in the blast zone of a potential explosion. Had this been done, the two workers in the control room would not have been killed in the explosion.
Our experts are ready to help.